Quality Control
Quality Control Activities
The highest mission of NuFlare Technology is to deliver products, systems, and services that customers can use safely and comfortably in accordance with our quality policies. We endeavor to improve quality from the customer’s point of view. We aim to enhance our sensitivity and speed up our response to potential risk factors in order to eliminate product accidents and achieve the No.1 position for customer satisfaction.
NuFlare Technology Standards of Conduct(151 KB)
Quality Policies
- NuFlare Technology shall assure quality from the customer’s point of view.
- NuFlare Technology shall respect the rights of customers and third parties, as well as observe related laws, regulations, and contracts.
- NuFlare Technology shall establish a quality system that aims to perform total inspection.
- All departments and all members of NuFlare Technology shall join forces to achieve high built-in quality.
- NuFlare Technology shall endeavor to locate root causes to aim for fundamental improvements while endeavoring to prevent quality incidents through risk analysis.
- NuFlare Technology shall collect, analyze, and adequately disclose information in order to prevent quality incidents.
Quality Control Framework
NuFlare Technology's quality assurance activities are conducted under the overall supervision of the director in charge of the Quality Assurance Department (hereinafter referred to as "Chief Quality Executive") and the Quality Assurance Department, with the President taking responsibility. At NuFlare Technology, to improve quality throughout the product lifecycle from planning, development, and production to disposal and recycling, the "Chief Quality Executive" guides and audits the domestic and overseas plants and offices under his jurisdiction, as well as suppliers, maintenance and service companies, and contract manufacturing companies.
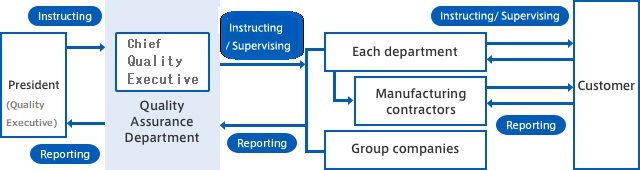
Initiatives for Improving Quality Management Capability
To raise its quality management capabilities, NuFlare Technology is committed to activities in four areas, focusing on a quality management system(QMS)based on ISO 9001. To this end, we constantly strive to enhance the quality of our designs and procured goods in order to eliminate major causes of defects while developing human resources who can help to further enhance our quality management capabilities. All of our initiatives are based on compliance.
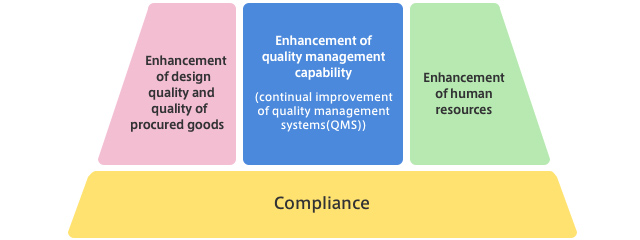
Development of People Who can Contribute to the Improvement of Quality
All departments of NuFlare Technology provide quality-assurance-related education to promote the “development of people who can contribute to the improvement of quality.” Different departments plan and implement different educational programs designed to help increase awareness of the importance of quality management, as well as reliability technology- and quality control-related skills, required of their respective roles and functions. The aim of “education for quality management human resources” is to provide quality management education, including that on cause analysis and preventative methods, to departments that are involved in the lifecycles of products.We also focus on compliance education, providing training on relevant laws and regulations and a quality mindset.
Enhancing the Quality Management System (QMS)
NuFlare Technology has acquired ISO 9001 certification as a basis for its quality management system. In addition, as part of its efforts to enhance its effectiveness, NuFlare Technology assesses the maturity of its quality management system to identify its issues and devise a plan to resolve them.
Standard against the implemented audit | JIS Q 9001 : 2015 (ISO9001 : 2015) |
---|---|
Registered Client | NuFlare Technology, Inc. |
Registration number | JUSE-RA-2109 |
Date of Initial Registration | May 17,1996 |
Reviewing agency | Union of Japanese Scientists and Engineers(JUSE) |
Scope of registration held | 1.Design, development, manufacturing, OEM (Original Equipment manufacturing) management and maintenance/service management of Electron Beam Mask Writers 2.Design, development, manufacturing and maintenance/service management of Optical Mask Inspection Systems 3.Design, development, OEM (Original Equipment Manufacturing) management and maintenance/service management of Epitaxial Reactors 4.Design and development of Electron Beam Mask Inspection Systems |
Period of Validity | December 1, 2023 ~ November 30, 2026 |
Ensuring the Quality of Procured Products
With the increasing complexity and globalization of procurement channels in recent years, product failures and accidents caused by "silent changes," where the specifications of procured products are changed and delivered without notice to the ordering party, have become a serious problem. In general, suppliers are important partners of ordering parties, and for NuFlare Technology, the quality of suppliers is becoming increasingly important for our business management. To maintain and improve the quality of the procured products, NuFlare Technology concludes a quality assurance agreement with key suppliers that describes its concept of quality assurance and quality requirements. At NuFlare Technology, the procurement, quality, and engineering departments concerned cooperate to audit our suppliers at appropriate intervals according to the types and importance of the procured products.red products.
Disclosure of Quality Information
If any quality-related problems that could affect the safety of customers should be identified, NuFlare Technology will inform all customers, without any delay, as well as disclose information about them through the website of NuFlare Technology and by other means.
As for other quality-related information such as information about changes in parts that are used, we will provide such information to customers in accordance with contracts with customers, relevant laws and regulations (Export Trade Control Order etc), and the like.
Product security management system
To ensure the security of our products, systems, and services, we are working to ensure security in the product development process under our product security management system.